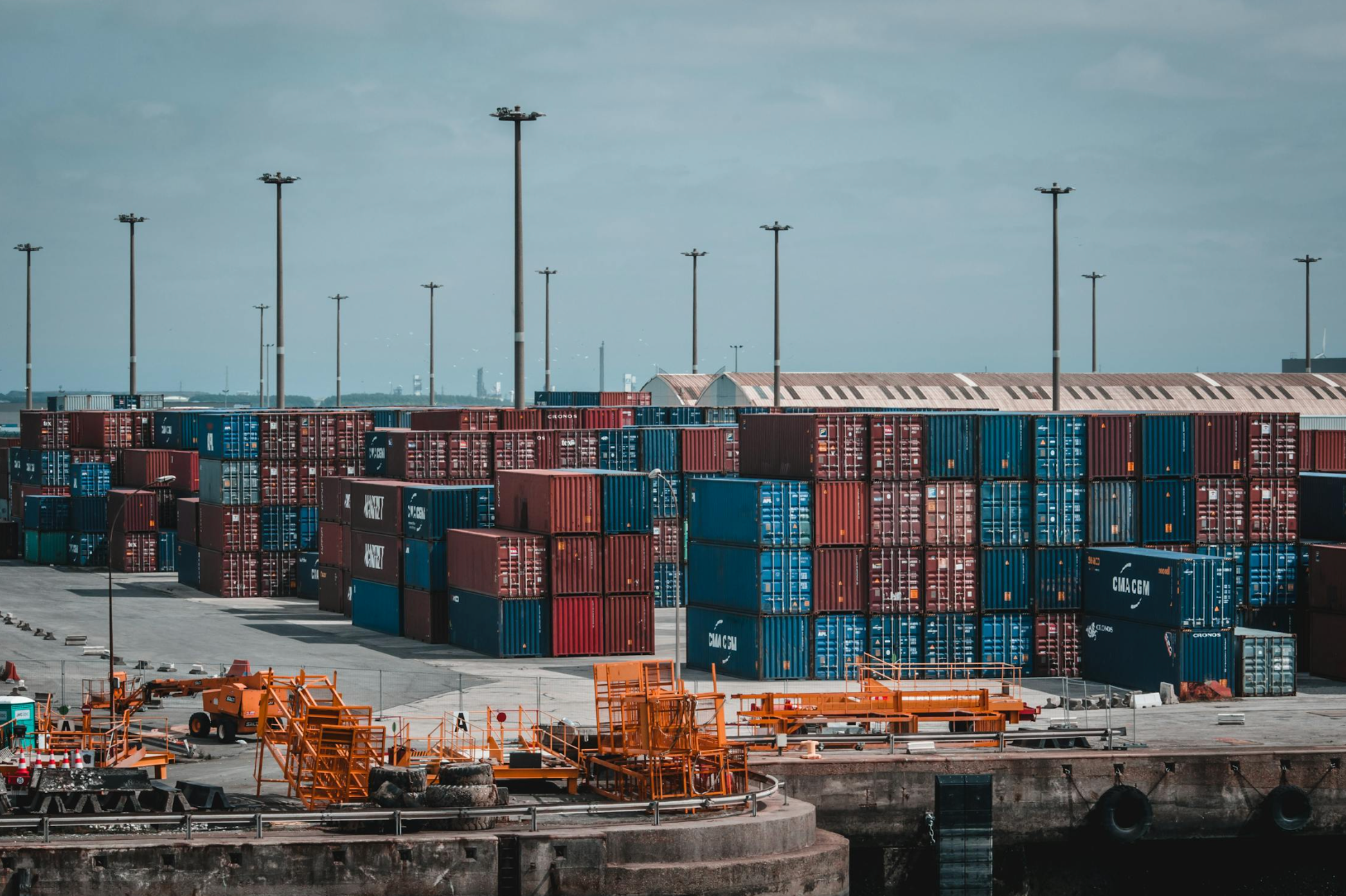
Nearly every industry is experiencing shifts in today’s global economy, and the metal fabrication and fastener sector is no exception.
With the U.S. expanding tariffs on imported steel, aluminum, and fasteners—including under Section 232 and related trade actions—the ripple effect has been swift and far-reaching. For manufacturers, construction firms, and infrastructure developers, this means rising costs, supply chain disruptions, and mounting pressure to source smarter and closer to home.
Rising Material Costs—Across the Board
At the core of the issue is the escalating cost of raw materials. Whether steel is sourced domestically or internationally, the imposition of tariffs has pushed prices higher industry-wide. As of Q1 2025, benchmark prices for shredded scrap have increased by over 12% year-over-year, according to data from SteelBenchmarker and Fastmarkets AMM. Meanwhile, hot-rolled coil prices remain volatile, hovering above $960/ton—a 15–18% increase compared to pre-tariff levels.
For fabricators, this means tighter margins and increased operating expenses. Precision fasteners, anchor bolts, washers, and structural components—especially those made from stainless steel, alloy steel, or heat-treated grades—are now associated with significant price premiums.
Imported Equipment Also Hit
Beyond materials, many fabrication shops rely on imported CNC machines, hydraulic presses, and even fastening hardware that now fall under updated tariff schedules. While some exemptions exist through product-specific exclusions and quota arrangements, these are often inconsistent and slow to process. For small and mid-size shops operating with lean capital budgets, these equipment price hikes can stall investment in automation and innovation.
Disrupted Supply Chains and Domestic Bottlenecks
Tariffs have also caused a significant reshuffling of global supply chains. Without broad exemptions for allied nations or fastener subcategories, companies have been forced to turn to alternative or domestic sources. However, this shift has exposed constraints within the U.S. supply base. Domestic producers are under strain due to labor shortages, limited mill capacity, and rising regulatory compliance costs. Some flat roll mills are operating at over 85% capacity, yet lead times for certain structural components have stretched beyond 10 weeks.
The result? Longer lead times, constrained inventory, and greater uncertainty throughout the production chain.
A Competitive Edge for U.S. Manufacturers
Despite these challenges, opportunities are emerging—especially for U.S.-based fabricators like Threadline Products. With tariffs narrowing the cost gap between domestic and international suppliers, it’s now often more economical and efficient to partner with American manufacturers than to rely on imports.
Threadline offers a full range of domestically fabricated structural hardware, including anchor bolt sleeves, tie rods, deformed bars, weld studs, and plate washers—all produced at our Charlotte, NC facility. Our geographic proximity, production agility, and responsive customer service give contractors and OEMs a tangible edge when every day and dollar counts.
More Control, Better Compliance
By sourcing domestically, customers gain more than just faster turnaround—they gain enhanced control over quality assurance, logistics, and regulatory compliance. This is especially critical in high-stakes industries like infrastructure, energy, and heavy construction, where documentation (e.g., MTRs), on-time delivery, and spec compliance can’t be compromised.
With Threadline’s rapid quoting process, short lead times, and full documentation packages, our partners can keep projects moving forward despite today’s unpredictable global landscape.
Looking Ahead
As the steel tariff landscape continues to evolve, one thing remains clear: investing in reliable American manufacturing partners is no longer just patriotic—it’s practical.
Let’s Keep Your Project Moving
Need help sourcing high-quality, domestic metal hardware?
Contact Threadline Products today for a fast quote, and discover how we’re helping fabricators, contractors, and OEMs stay ahead in a volatile market. Ask about our current lead times and documentation packages tailored to your project requirements.